Understanding the Salt Spray Test for Marine Searchlights
Table of Contents
Marine searchlights operate in some of the most challenging environments on Earth, constantly exposed to harsh weather, salty air, and corrosive conditions. Ensuring their durability and reliability requires rigorous testing, among which salt spray testing (or salt fog testing) plays a crucial role. This article delves into what salt spray testing is, why it’s critical for marine searchlights, how it’s conducted, and other essential tests these products undergo.
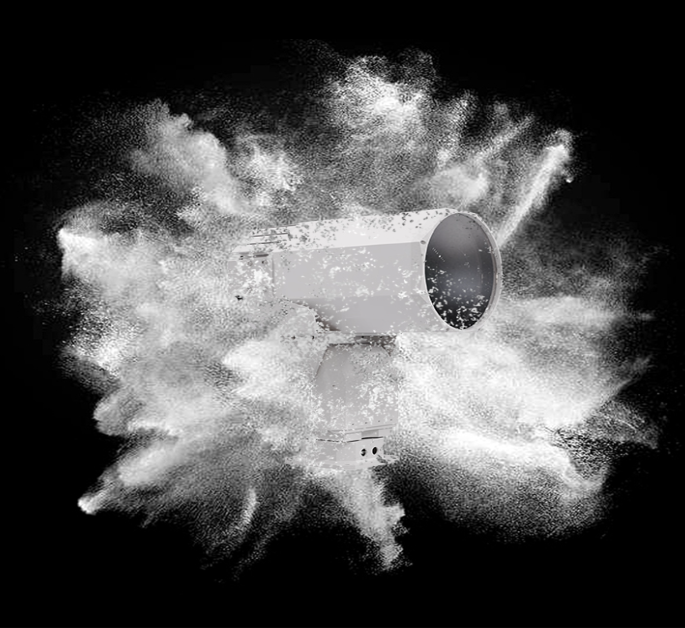
What Is Salt Spray Testing
Salt spray testing is a standardized method used to evaluate the corrosion resistance of materials and coatings. In this test, a sample is exposed to a salt-laden mist inside a controlled chamber, replicating the harsh conditions typical of marine environments. The duration of the test can vary depending on the material’s intended application and corrosion resistance standards.
Common standards for salt fog testing include ASTM B117 and ISO 9227, which provide detailed protocols to ensure consistent and reproducible results. By simulating long-term exposure to saltwater in a condensed timeframe, this test helps manufacturers assess a product’s resilience against corrosion.
Why Do Marine Searchlights Need Salt Spray Testing
Marine searchlights are exposed to salty sea air, humidity, and frequent splashes of seawater. Without proper corrosion resistance, these factors can compromise the structural integrity and performance of the lights. Salt fog testing ensures that:
Reason | Importance | Role of Salt Spray Testing |
Corrosion Resistance Verification | The salty air and humidity in the marine environment accelerate the corrosion of metals and coatings, leading to material degradation and equipment failure. | Simulates a salt-laden environment to test material and coating resistance, ensuring suitability for long-term marine use. |
Ensuring Structural Integrity | Corrosion can weaken critical components such as housings and brackets, leading to structural failures, especially in rough sea conditions. | Identifies material weaknesses and ensures the structure can withstand prolonged exposure to corrosive elements. |
Protecting Internal Electrical Systems | Corrosion may compromise seals, allowing saltwater or moisture to enter and damage circuits, LEDs, or other electrical components. | Ensures housings and seals effectively protect internal components, maintaining electrical reliability. |
Maintaining Optical Performance | Reflective surfaces and lenses may lose reflectivity or transparency due to corrosion, resulting in uneven or reduced light output. | Verifies the durability of optical materials and coatings, ensuring consistent light performance over time. |
Reducing Maintenance Costs | Frequent repairs or replacements of corroded components increase operational costs, particularly for vessels far from maintenance facilities. | Ensures product durability, reducing maintenance frequency and replacement costs, improving operational efficiency. |
Meeting Safety Requirements | In emergencies (e.g., search-and-rescue or adverse weather), failure of the searchlight could jeopardize crew and vessel safety. | Confirms the searchlight’s reliability during critical situations, enhancing navigation and operational safety. |
Building Customer Confidence | Customers require durable and reliable products, especially for marine environments, with strict demands on performance and lifespan. | Proves product quality and reliability, boosting brand reputation and customer trust. |
How Is Salt Spray Testing Conducted
Salt spray testing typically involves the following steps:
Preparing the Test Samples
Before the salt spray test begins, marine searchlights or their components are carefully prepared:
- Selection of Components: Key parts, such as housings, brackets, fasteners, and optical components, are chosen for testing. In some cases, the entire assembled searchlight is tested.
- Cleaning: The test samples are cleaned to remove any grease, dust, or other contaminants that could affect test results.
- Mounting: The samples are mounted in the test chamber in such a way that all critical surfaces are exposed to the salt spray.
Setting Up the Salt Spray Test Chamber
The salt spray test is conducted in a specialized chamber designed to simulate a corrosive marine environment:
- Test Chamber Environment: The chamber is maintained at a constant temperature, typically around 35°C (95°F), and filled with a saline mist.
- Saline Solution: A solution of sodium chloride (NaCl) and distilled water is used, with a concentration typically around 5% (similar to seawater).
- Spray Mechanism: The saline solution is atomized into a fine mist using compressed air, creating a uniform salt fog that settles on the test samples.
Test Duration and Cycles
The duration of the salt spray test depends on the specific standards being followed and the intended application of the searchlight:
- Standard Test Durations: Common durations include 24, 48, 96, or even up to 1,000 hours, depending on the desired level of corrosion resistance.
- Cyclic Testing: Some tests involve alternating between salt spray exposure and drying cycles to simulate real-world conditions more accurately.
Monitoring During the Test
Throughout the test, key parameters are monitored to ensure consistency and reliability:
- Temperature Control: The chamber’s internal temperature is continuously measured and regulated.
- Salinity Levels: The concentration of the saline solution is regularly checked to maintain accuracy.
- Spray Rate: The amount of salt fog settling on the samples is monitored to meet the required specifications.
Post-Test Inspection
After the test duration is complete, the samples are carefully examined for signs of corrosion or other forms of degradation:
- Visual Inspection: Technicians look for rust, pitting, peeling coatings, or discoloration on the surfaces.
- Functional Testing: If the entire searchlight was tested, its functionality (e.g., light output, structural stability) is assessed to ensure performance remains unaffected.
- Coating Analysis: The thickness and adhesion of protective coatings may be tested to evaluate their effectiveness.
Test Standards and Certifications
Salt spray tests are performed in accordance with international standards to ensure consistency and reliability. Common standards include:
- ASTM B117: Widely used for evaluating corrosion resistance in marine environments.
- ISO 9227: A global standard specifying methods for salt fog testing.
- Custom Specifications: Some manufacturers or customers may require additional test parameters tailored to specific needs.
Reporting and Improvement
The results of the salt spray test are documented in detailed reports:
- Performance Analysis: Data on corrosion resistance, coating durability, and structural integrity are compiled.
- Product Optimization: If deficiencies are identified, materials or designs may be revised to improve the product’s resistance to corrosion.
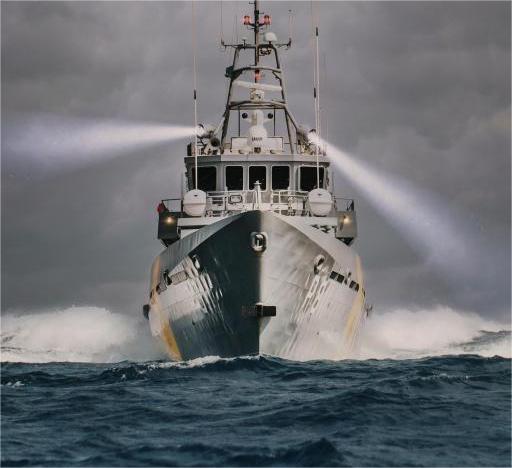
Challenges in Conducting Salt Spray Tests in Practice
Simulating Real-World Conditions
While salt fog testing creates a highly corrosive environment, it doesn’t fully replicate the diverse factors present in real marine environments, such as temperature fluctuations, UV exposure, and varying humidity levels. This can sometimes limit the test’s predictive accuracy for long-term performance.
Standardization Limitations
International standards like ASTM B117 and ISO 9227 provide guidelines, but their broad criteria may not account for specific material properties or niche application requirements. Manufacturers often need to supplement these tests with additional procedures.
Environmental Concerns
The disposal of saline solutions and other test byproducts must be managed responsibly to minimize environmental impact. This requires extra effort in compliance and waste management.
Time and Resource Intensive
Long-duration tests (e.g., 1,000 hours or more) consume significant resources, including energy, materials, and technician oversight, making them costly for manufacturers with tight production timelines.
Other Essential Tests for Marine Searchlights
While salt fog testing is vital, marine searchlights must also undergo other rigorous evaluations to ensure top performance:
- Vibration Testing: Simulates the mechanical stress of waves and engine vibrations to ensure stability.
- Thermal Testing: Verifies performance in extreme temperatures, both hot and cold.
- IP Rating Tests: Assesses resistance to water and dust ingress, critical for marine environments.
- UV Resistance Testing: Ensures that materials and coatings do not degrade under prolonged sunlight exposure.
- Shock Testing: Evaluates durability against sudden impacts or rough handling.
Salt spray testing is not only an important part of the production process of marine searchlights, but also a core means to ensure their performance and reliability. Under long-term exposure to the harsh marine environment, searchlights that pass the salt spray test can effectively resist corrosion and ensure structural integrity, optical performance and stability of the electrical system. For Yushuo, the salt spray test not only reflects the commitment to quality, but also brings confidence and value to customers. Choosing a marine searchlight that has passed rigorous testing is not only a reliable guarantee, but also a responsibility for future navigation safety.