Specific Classification of Explosion Proof Light Fixture
Table of Contents
In the world of industrial safety, lighting plays a crucial role that extends beyond mere illumination—it ensures protection, efficiency, and compliance in hazardous environments. Explosion proof light fixture, a sophisticated blend of engineering and innovation, is designed to prevent ignition risks in volatile settings. From safeguarding coal mines to ensuring visibility in oil refineries, these lights are tailored to meet stringent safety standards.
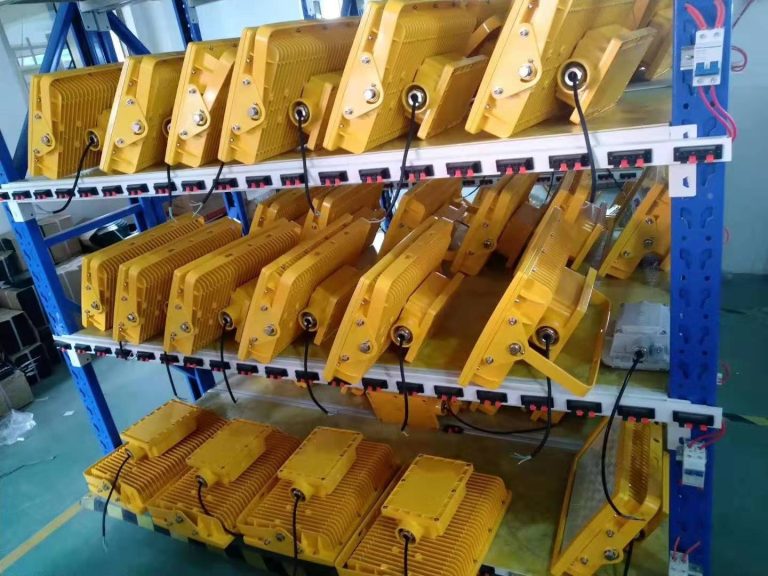
Classification by Explosion-proof Level
The explosion-proof level is usually determined according to the International Electrotechnical Commission (IEC) standards and ATEX specifications. The core is to avoid the risk of ignition in explosive gas or dust environments through measures such as lamp structure and electrical performance. It is mainly divided into the following three categories:
Explosion-proof Level | Applicable Standard | Application Scenario |
Category Ⅰ | Mine explosion-proof (Ex ia, Ex ib) | Underground coal mines, high gas concentrations |
Category Ⅱ | Industrial explosion-proof (Ex d, Ex e, etc.) | Chemical plants, paint spray booths, oil depots |
Category Ⅲ | Combustible dust explosion-proof (Zone 20, 21, 22) | Flour mills, woodworking plants, textile factories |
Characteristics and Applications of Different Levels of Explosion Proof Light Fixtures
Explosion-proof lighting is tailored to meet the specific requirements of different hazardous environments. The characteristics and applications of lighting vary across the three main explosion-proof categories: CategoryⅠ, CategoryⅡ, and CategoryⅢ. Below is a comprehensive exploration of each grade, highlighting their unique features and practical uses.
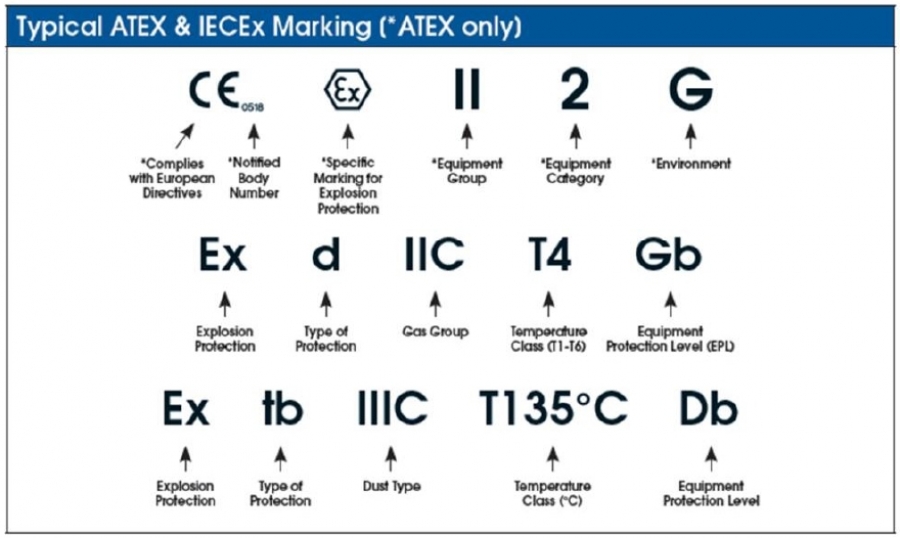
Explosion-proof Categories | Key Characteristics | Applications |
Category Ⅰ | Enhanced Explosion Resistance: Built to withstand explosive methane gas (commonly found in coal mines) and coal dust. | Underground Coal Mines: Provides stable lighting for work faces, tunnels, and operational areas. |
Low Voltage Operation: Typically operates on 12V or 24V to minimize the risk of sparking. | ||
Robust Design: Features a fully sealed structure with high IP ratings (commonly IP68) to resist water, dust, and extreme environmental conditions. | Mining Machinery: Installed on equipment like conveyors and drills for safe illumination. | |
Durable Materials: Constructed with anti-corrosive and high-strength materials to endure harsh underground environments. | ||
Category Ⅱ | Versatility: Designed for explosive gas atmospheres (Zones 1 and 2), such as petrochemical plants and spray booths. | Petrochemical Plants: Provides reliable lighting in areas with volatile gases and flammable vapors. |
Explosion-Proof Mechanism: Incorporates flameproof (Ex d), increased safety (Ex e), or intrinsic safety (Ex i) designs to contain potential internal ignition. | Oil Depots and Storage Tanks: Ensures safe operations in facilities prone to gas leakage risks. | |
Wide Voltage Range: Compatible with 100-240V AC for use in various industrial facilities. | Hazardous Material Warehouses: Offers illumination in spaces storing flammable or reactive substances. | |
Enhanced Durability: Features high-temperature resistance, anti-corrosion coatings, and shock-resistant designs. | ||
Category Ⅲ | Dust Explosion Prevention: Specifically designed to prevent ignition in areas with combustible dust (Zones 20, 21, and 22). | Food Processing Plants: Used in flour mills and grain storage areas where fine particles pose explosion risks. |
Sealed Construction: Fully enclosed to prevent dust accumulation and ensure efficient heat dissipation. | Woodworking Factories: Ensures safe illumination in facilities with sawdust and wood particles. | |
Temperature Control: Incorporates thermal management systems to avoid surface overheating. | Textile Manufacturing: Provides dust-proof lighting in environments with lint and fiber build-up. | |
Energy Efficiency: Often equipped with LED technology for long-lasting and energy-efficient operation. |
Technical Parameters Example
Specification | Category Ⅰ | Category Ⅱ | Category Ⅲ |
Voltage | 12V/24V | 100-240V | 220V |
Ingress Protection | IP68 | IP66~IP68 | IP66 |
Lighting Range | ≥200 meters | WF2 | ≤85°C |
Relationship Between Explosion Proof Light Fixture Levels and Industrial Safety Regulations
Industrial standards (such as ATEX and NEC) not only guide the manufacture of lamps, but also regulate the use scenarios. The choice of explosion-proof level is directly related to the company’s safe production and legal compliance.
Industrial Specifications | Applicable environment | Recommended level |
ATEX Zone 1 | High risk explosion area | Class Ⅱ or above |
ATEX Zone 2 | Medium risk area | Category Ⅱ |
NEC Class Ⅱ | Dust explosion risk | Category Ⅲ |
Safety First: Preventing Ignition
Explosion-proof lighting grades are meticulously designed to contain any sparks, heat, or arcs that could ignite surrounding hazardous materials. This directly aligns with industrial safety standards, which prioritize ignition prevention. For instance:
IEC 60079 requires enclosures to be capable of withstanding internal explosions without transmitting pressure to the external environment.
Compliance Mandates
Many industries are legally required to comply with specific explosion-proof standards. Adhering to the correct lighting grade ensures compliance with regulations like:
OSHA (Occupational Safety and Health Administration) in the U.S.
ATEX Directive 2014/34/EU in Europe.
Customized Safety Solutions
Different industrial sectors have unique explosion risks. For example:
Oil and Gas: Zone 0 and Zone 1 lighting is critical due to the continuous presence of flammable gases.
Agriculture: Dust Zone 20 lighting is essential in grain handling facilities.
Classification by Lighting Type
The choice of explosion-proof lighting type depends on the specific requirements of the hazardous environment, balancing safety, efficiency, and cost-effectiveness. From energy-efficient LED to eco-friendly solar solutions, each type serves a unique purpose in illuminating and safeguarding high-risk areas.
Lighting Type | Key Features | Advantages | Disadvantages | Applications |
LED Lighting | Low energy consumption, long lifespan, excellent thermal management; directional light for focused illumination | Energy Efficient: Saves up to 70% energy | High Initial Cost: Expensive upfront | Oil and gas platforms, chemical plants, underground mines where high-efficiency and stable light is needed |
Long Lifespan: Over 50,000 hours | Requires Thermal Management | |||
Durable: Shock-resistant for harsh environments | ||||
Fluorescent Lighting | Uniform light distribution, suitable for large-area general lighting; simple design and low maintenance cost | Low Cost: Budget-friendly | Short Lifespan: Typically 8,000–12,000 hours | Warehouses, workshops, hazardous storage areas requiring uniform lighting |
Soft Light: Reduces glare effects | Lower Durability: Unsuitable for extreme temperatures | |||
Gas Discharge Lighting | High intensity, suitable for outdoor and high-ceiling applications; robust explosion-proof housing design | High Brightness: Ideal for large areas | Long Startup Time: Slow warm-up | Refineries, ports, large outdoor spaces, and high-ceiling areas |
Good Voltage Tolerance: Suitable for fluctuating voltage environments | High Energy Consumption: Consumes more power than LEDs | |||
Fiber Optic Lighting | Isolates the light source from hazardous zones, avoiding heat generation; flexible routing for confined or hard-to-reach areas | Intrinsically Safe: No heat, reducing ignition risk | Complex Installation: Higher initial costs for setup | Control rooms, confined spaces, environments storing sensitive or explosive materials |
Flexible Installation: Suitable for complex spaces | Limited Brightness: Unsuitable for high-brightness areas | |||
Solar-Powered Lighting | Uses renewable energy, suitable for remote locations; equipped with batteries for continuous lighting during low-light conditions | Eco-Friendly: Reduces carbon footprint | Weather-Dependent: Performance affected by low sunlight | Remote construction sites, offshore platforms, emergency lighting situations |
Off-Grid Operation: Works in areas without power supply | Limited Storage: Battery capacity restricts runtime |
Classification of by Energy Source
Explosion proof light fixture is a critical component in hazardous environments, ensuring safety and reliability. Based on energy sources, these lighting systems can be classified into several types, each offering distinct advantages tailored to specific industrial needs.
Detailed Advantages and Applications of Each Energy Source
Energy Source | Key Features | Advantages | Applications |
Electric-Powered | Traditional wired power supply, drawing electricity from the grid. | Reliable: Uninterrupted power supply | Factories, refineries, and industrial plants with stable power grids. |
Widely Available: Compatible with most setups. | |||
Battery-Powered | Operates using rechargeable or replaceable batteries. | Portable: Easy to move | Emergency lighting, remote sites, or temporary installations. |
Independent: Works in areas without grid connectivity. | |||
Solar-Powered | Utilizes solar panels to convert sunlight into electricity, often combined with battery storage. | Eco-Friendly: Zero emissions | Offshore platforms, outdoor installations, remote construction sites. |
Off-Grid Capability: Ideal for remote locations. | |||
Hybrid-Powered | Combines solar energy with grid or battery backup for enhanced reliability. | Versatile: Ensures continuous lighting | Locations with intermittent sunlight or variable energy needs. |
Cost-Efficient: Reduces dependency on the grid. | |||
Fuel-Powered (Diesel/Generator) | Uses diesel or gas generators to power the lighting system. | High Output: Suitable for high-power needs | Large-scale outdoor projects, emergency response setups, or locations with no stable electricity supply. |
Independent: Operates without a grid. |
Comparative Overview
Parameter | Electric-Powered | Battery-Powered | Solar-Powered | Hybrid-Powered | Fuel-Powered |
Reliability | High | Moderate | Weather-Dependent | Very High | Very High |
Portability | Low | High | High | Moderate | High |
Eco-Friendliness | Moderate | Moderate | High | High | Low |
Cost Efficiency | High (long term) | High | High (low OPEX) | Moderate (dual setup) | Low (high OPEX) |
Setup Complexity | Low | Low | Moderate | High | Moderate |
Selecting the right energy source for explosion proof light fixture requires careful consideration of operational needs, environmental conditions, and cost constraints. Each energy type offers unique advantages tailored to specific applications, ensuring safety, efficiency, and compliance in hazardous environments.
Classification by Installation Method and Applicability Evaluation
Explosion proof light fixture can be classified by installation methods, each designed for specific environments and requirements. Choosing the correct installation type enhances safety, efficiency, and functionality.
Classification by Installation Method
Installation Method | Key Features | Advantages | Limitations | Typical Applications |
Wall-Mounted | Fixed on walls to provide directional lighting; often adjustable for targeting specific areas. | Space-Saving: Ideal for narrow spaces | Limited Coverage: May not illuminate large areas effectively. | Control rooms, corridors, workshops where wall-mounted lighting enhances visibility. |
Adjustable: Can focus on specific areas. | ||||
Ceiling-Mounted | Installed directly on ceilings, providing broad and uniform illumination. | Wide Coverage: Uniform lighting for large areas. | Fixed Position: Cannot adjust the direction easily. | Warehouses, factories, chemical plants requiring consistent overhead lighting. |
Permanent Setup: Reduces maintenance. | ||||
Floor-Standing | Portable or fixed on the ground, providing flexible lighting solutions for varying needs. | Versatile: Can be moved to different locations. | Takes Space: Occupies floor area, potentially causing obstruction. | Construction sites, outdoor workspaces, temporary industrial lighting setups. |
High Output: Suitable for large-scale tasks. | ||||
Recessed | Built into ceilings, walls, or floors for a seamless and integrated appearance. | Aesthetic: Minimalistic design. | Complex Installation: Requires pre-designed spaces and additional construction work. | Cleanrooms, laboratories, hazardous environments needing seamless lighting. |
Durable: Protected from physical damage. | ||||
Suspended | Hung from ceilings or beams using chains or rods, often used in high-ceiling environments. | Adjustable Height: Suitable for varying installation heights. | Requires Support: Needs sturdy mounting points. | Factories, warehouses, offshore platforms with high ceilings. |
Effective Spread: Covers large areas. | ||||
Handheld | Portable and lightweight, designed for mobility and temporary use in hazardous areas. | Highly Portable: Easy to carry and use. | Limited Runtime: Depends on battery capacity or temporary power sources. | Emergency repairs, confined spaces, field inspections, and temporary hazardous zone lighting. |
Quick Deployment: No need for fixed installation. |
Applicability Evaluation of Installation Methods
Installation Method | Advantages | Best For |
Wall-Mounted | Ideal for localized tasks or areas with limited floor space. Adjustable designs improve focus on specific zones. | Environments requiring targeted illumination, such as control panels or workstations. |
Ceiling-Mounted | Excellent for general lighting in large, open areas. Installation ensures minimal obstruction. | Industrial plants, chemical storage areas, and manufacturing floors requiring consistent overhead lighting. |
Floor-Standing | Provides flexibility for tasks that require temporary or mobile light sources. High-power models illuminate vast outdoor spaces effectively. | Temporary setups in construction sites, oil refineries, or emergency response scenarios. |
Recessed | Integrated design reduces clutter and risk of accidental damage. Perfect for controlled environments. | Laboratories, cleanrooms, and industrial environments with strict hygiene or space constraints. |
Suspended | Adjustable height and wide coverage make it suitable for large-scale operations. | High-ceiling environments such as warehouses, offshore platforms, and power plants. |
Handheld | Provides maximum flexibility and mobility for urgent or localized lighting needs. | Field operations, confined spaces, and emergency situations requiring quick and portable solutions. |
Comparative Analysis
Parameter | Wall-Mounted | Ceiling-Mounted | Floor-Standing | Recessed | Suspended | Handheld |
Mobility | Low | Low | High | Low | Moderate | Very High |
Coverage | Moderate | High | High | Moderate | Very High | Low |
Aesthetic Integration | Moderate | Moderate | Low | High | Moderate | Low |
Ease of Installation | Moderate | Moderate | High | Low | Moderate | Very High |
Best For | Focused tasks | General lighting | Temporary setups | Seamless design | Large areas | Emergency use |
Recommendations
- For targeted lighting needs: Wall-mounted or handheld options are best.
- For general illumination in large spaces: Ceiling-mounted or suspended installations are ideal.
- For temporary setups: Floor-standing or handheld lighting offers excellent flexibility.
- For high-aesthetic or controlled environments: Recessed lighting is the top choice.
The installation method for explosion proof light fixture must align with the specific requirements of the environment to ensure optimal performance and safety. Proper evaluation of each type’s features and advantages helps in making the right choice for diverse industrial and hazardous settings.
Explosion-proof lighting is not just a technical necessity but a cornerstone of industrial safety and efficiency. By understanding its classifications and applications, businesses can ensure compliance with stringent safety standards while optimizing performance in hazardous environments. Whether you require LED solutions for energy efficiency, solar-powered options for remote areas, or handheld devices for emergency use, choosing the right explosion-proof lighting system is critical.
At Yushuo, we pride ourselves on offering cutting-edge explosion-proof lighting solutions that combine durability, performance, and innovation. With a commitment to safety and quality, Yushuo lighting products are engineered to excel in even the most demanding environments, ensuring that your operations remain safe, efficient, and compliant. Illuminate your hazardous spaces with confidence—choose Yushuo, your trusted partner in industrial lighting.