How Zoning and Classification Affect Marine Explosion-proof Lighting
Marine environments often present a unique combination of hazards, ranging from corrosive saltwater exposure to the presence of flammable gases and vapors, especially on oil tankers, chemical carriers, offshore platforms, and port facilities. In such settings, marine explosion-proof lighting becomes a critical safety requirement. Proper zoning and classification help ensure that lighting systems are correctly selected and installed to prevent ignition of explosive atmospheres while withstanding harsh marine conditions. This article provides an overview of how hazardous locations are zoned and classified and how these classifications influence the selection of explosion-proof lighting.
Table of Contents
Why Explosion-proof Lighting is Crucial in Marine Applications
Explosion-proof lighting in marine environments is designed to operate safely in areas where explosive gases or vapors may be present due to cargo operations, fuel storage, or maintenance procedures. The design ensures that even if a fault occurs inside the fixture, such as a spark, it will not ignite the external atmosphere. Beyond safety, marine explosion-proof lighting must also provide resistance to salt corrosion, moisture ingress, and temperature extremes.
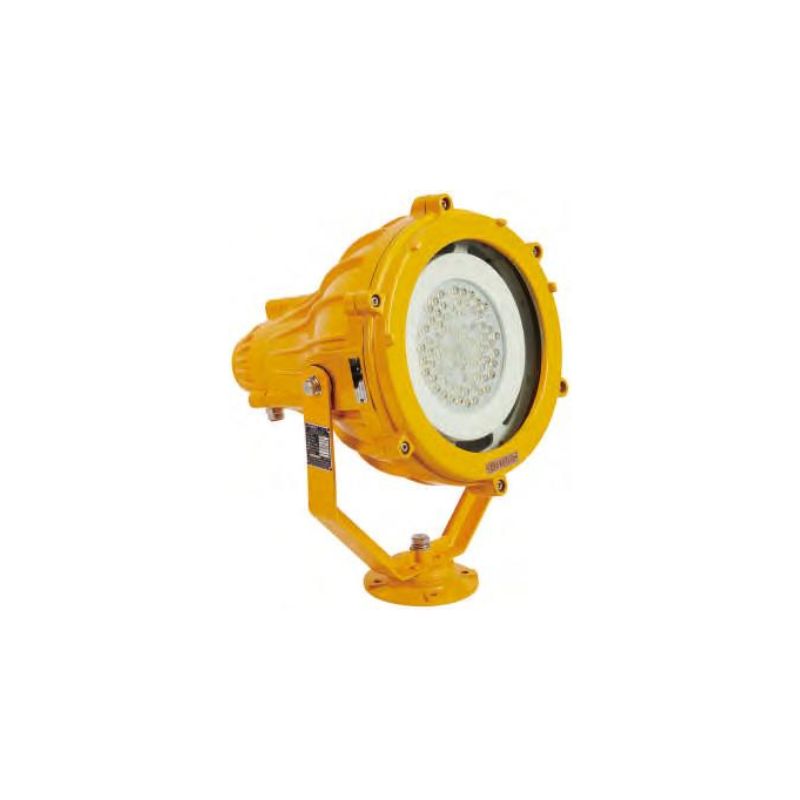
Marine Hazardous Area Zoning (IEC/ATEX Framework)
Gas Atmospheres (Zone 0, 1, 2):
Zone | Type of Hazard | Description | Typical Marine Examples |
Zone 0 | Gas/Vapor | Pump rooms, vent risers, and tank deck around openings | Inside cargo tanks, vapor recovery lines |
Zone 1 | Gas/Vapor | An explosive gas atmosphere is likely during normal operations | Pump rooms, vent risers, tank deck around openings |
Zone 2 | Gas/Vapor | An explosive gas atmosphere is unlikely during normal operations, short duration | Machinery spaces near fuel lines, areas around vents |
Dust Atmospheres (Zone 20, 21, 22):
Zone | Type of Hazard | Description | Typical Marine Examples |
Zone 20 | Dust | Combustible dust is likely during normal operation | Inside grain silos, enclosed hoppers onboard |
Zone 21 | Dust | Combustible dust is not likely in normal operation, short duration | Conveyor discharge areas, enclosed transfer points |
Zone 22 | Dust | Combustible dust not likely in normal operation, short duration | Machinery spaces with minor dust presence |
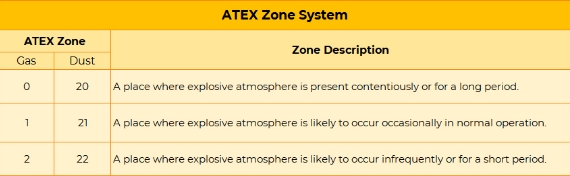
North American Marine Classification (NEC System)
This chart shows how hazardous marine areas are classified based on the NEC (National Electrical Code) system, which is widely used in the United States.
Class | Division | Description | Typical Marine Examples |
Class I | Division 1 | Flammable gases or vapors present during normal operation | Pump rooms, fuel storage tanks, loading manifolds |
Division 2 | Flammable gases or vapors not normally present, but may appear abnormally | Areas near ventilation outlets, machinery rooms | |
Class II | Division 1 | Combustible dust present during normal operation | Grain handling areas, enclosed cargo transfer zones |
Division 2 | Combustible dust infrequently present, and only under abnormal conditions | Engine room corners with dust buildup, ventilation ducts | |
Class III | Division 1 | Easily ignitable fibers handled or manufactured | Rare in marine but may include rope or textile areas |
Division 2 | Easily ignitable fibers stored only | Storage lockers for combustible textiles |
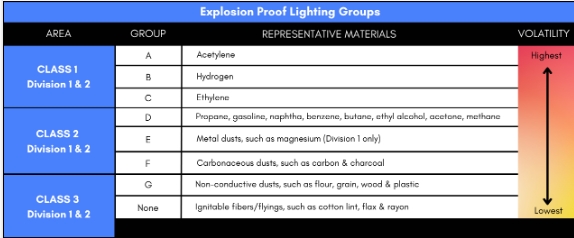
Selecting Explosion-proof Lighting Aligned with Zoning Classification and Marine Environmental Demands
Selecting explosion-proof lights for marine applications is a critical task that requires a balanced approach. It’s not enough to simply choose a fixture that meets explosion-proof standards and selection must align both with the designated hazardous zone classification and the challenging conditions unique to maritime settings.
1. Zoning Classification Compliance
Explosion-proof lighting must first be selected based on the specific hazardous area classification. According to the IEC/ATEX or NEC (North American) standards, marine hazardous zones are defined by the frequency and duration of the presence of explosive gases, vapors, or combustible dusts. For example:
- Zone 0 (IEC/ATEX) or Class I, Division 1 (NEC) indicates a continuous presence of explosive gas atmosphere.
- Zone 1 / Class I, Division 1 involves gases likely to occur during normal operations.
- Zone 2 / Class I, Division 2 covers areas where explosive atmospheres are less frequent and short-lived.
Lighting must be certified specifically for the zone it will be installed in, as each carries different risk levels and safety requirements. Marine installations must also factor in certifications from maritime authorities such as DNV, ABS, or Lloyd’s Register.
2. Resilience to Marine Environmental Stress
Once zoning compliance is ensured, lighting must be evaluated for its performance under severe marine conditions. The ocean environment is harsh—characterized by high salinity, humidity, UV exposure, temperature variations, and mechanical vibrations. To withstand these challenges:
- Corrosion resistance is paramount. Housings should be constructed of marine-grade aluminum, stainless steel, or specialized non-metallic composites.
- Ingress protection must be high, ideally rated IP66 or above, to prevent moisture and salt intrusion.
- Vibration and impact resistance is essential, especially for shipboard installations where constant motion and shock are unavoidable.
3. Thermal and Electrical Safety Alignment
Explosion-proof lighting must also manage heat effectively to prevent the surface from reaching ignition temperatures. Marine vessels often have confined spaces and limited ventilation, increasing the importance of:
- Efficient thermal management through built-in heat sinks or low-heat emission LEDs.
- Correct temperature class (T-rating), ensuring the surface temperature remains below the auto-ignition temperature of surrounding gases.
- Electrical compatibility, particularly in offshore rigs and ships that use DC or variable AC power systems, requiring fixtures with stable performance across fluctuating voltages.
4. Performance in Operational Visibility and Emergency Conditions
Safety in marine hazardous zones depends on reliable illumination. Lighting should deliver consistent output in low-visibility conditions like fog, oil mist, or enclosed compartments. Features to look for include:
- High-lumen, anti-glare illumination with wide beam distribution.
- Color temperature suitable for visual clarity (typically cool white LEDs).
- Emergency lighting functionality or battery backup in the event of power failure.
5. Ease of Maintenance and Long-Term Reliability
Given the logistical challenges of servicing equipment offshore or at sea, explosion-proof lighting must be durable with minimal maintenance needs. Long-life LED technology used in explosion-proof lights, corrosion-proof external hardware, and modular internal components contribute to reduced service intervals. Additionally, quick-access designs allow safe maintenance without compromising the explosion-proof seal.
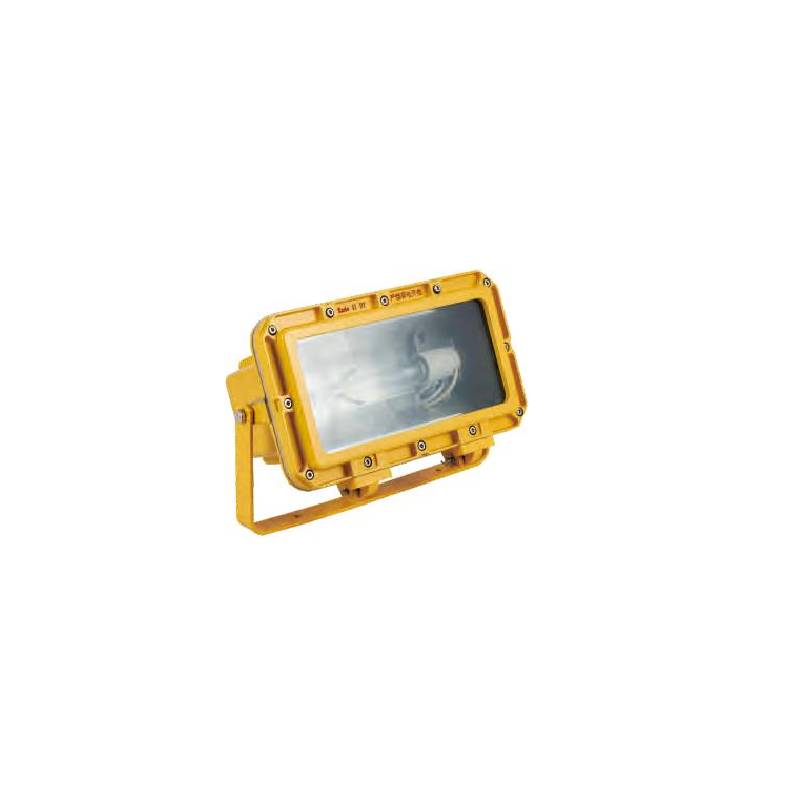
Common Applications of Explosion-proof Lighting in Marine Zones
- Pump Rooms
Pump rooms are among the most hazardous areas aboard marine vessels due to the presence of fuel vapors during loading, unloading, and transfer processes. These confined spaces often fall under Zone 1 or Class I, Division 1 classifications, where flammable gases are likely during regular operation. Explosion-proof lighting is essential here to eliminate ignition sources and ensure maintenance crews can work safely.
- Cargo Holds and Chemical Tank Storage Areas
Bulk carriers, tankers, and chemical ships often transport volatile cargo. The storage spaces, especially when handling petroleum products, chemicals, or grain, may develop combustible atmospheres. Explosion-proof lights, resistant to corrosion and ingress, are used extensively in these holds to allow safe inspection and monitoring, especially during cargo operations.
- Engine Rooms and Machinery Spaces
While not always classified as hazardous, engine rooms can become dangerous due to fuel leaks or vapors under abnormal conditions. In vessels powered by gas engines or dual-fuel systems, explosion-proof lighting is often required in designated machinery spaces to reduce the risk of fire from electrical sparks or overheating fixtures.
- Battery Rooms
Battery rooms aboard ships, especially those using lithium-ion or lead-acid batteries, can accumulate hydrogen gas—a highly explosive substance. These areas are typically categorized as hazardous (Zone 1 or Division 1), and explosion-proof lighting with adequate ventilation is mandated to prevent potential ignition from lighting systems.
- Deck Lighting in Tanker Vessels
On oil and chemical tankers, the open deck areas near cargo manifolds, vent pipes, and loading arms are exposed to vapor emissions during transfer operations. These are typically Zone 1 classified areas requiring robust explosion-proof floodlights or deck lights with excellent ingress protection and anti-corrosion coatings to withstand salt spray and harsh weather.
- Ventilation Shafts and Ducts
Ventilation ducts, especially those serving hazardous zones, can channel flammable vapors to lighting systems. Explosion-proof lighting is often installed within or near ventilation terminals to maintain visibility during maintenance while ensuring no ignition can occur if vapors accumulate.
- Offshore Oil and Gas Platforms
On offshore installations, most working areas are classified as hazardous. Drilling modules, production skids, gas processing areas, and helidecks require a full range of explosion-proof lighting, including high-bay fixtures, floodlights, and emergency luminaires. These lights must not only be explosion-proof but also marine-grade, able to withstand constant exposure to UV, salt, vibration, and impact.
- Shipboard Laboratories and Paint Lockers
Laboratories handling volatile solvents and paint lockers storing flammable materials are also classified hazardous zones on marine vessels. Explosion-proof lighting is installed in these enclosed, high-risk compartments to ensure safe access for crew and technicians without risking ignition from electrical components.
- Marine Fueling Stations and Terminals
Harbor fueling stations and transfer piers also fall under marine zoning regulations, especially during fuel bunkering and chemical offloading. These outdoor, often semi-permanent facilities require explosion-proof lighting for both safety and operational visibility during night operations.
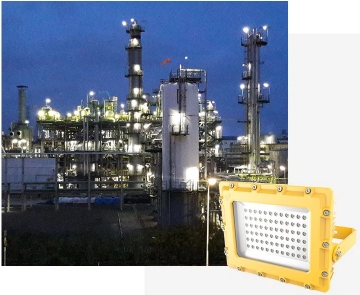
Best Practices for Compliance and Safety of Explosion-proof Lighting
This chart focuses on ensuring that explosion-proof lighting is compliant, properly maintained, and safe in hazardous locations.
Best Practice | Description |
Compliance with Industry Standards | Ensure that explosion-proof lighting meets standards such as ATEX (EU) or UL (USA), including certification for hazardous locations (Zone 1/2, Class I, II, or III). |
Proper Installation | Install lighting systems according to manufacturer instructions and ensure all wiring is adequately protected to prevent sparks in hazardous environments. |
Regular Inspection and Maintenance | Conduct routine inspections for signs of wear, corrosion, or damage, and replace faulty components promptly to prevent failure. |
Use of Correctly Rated Fixtures | Select lighting fixtures with appropriate ratings for the specific environment (e.g., temperature class, dust ingress protection) to prevent ignition of surrounding materials. |
Explosion-Proof Enclosures | Ensure that all enclosures are robust, sealed, and free from any cracks to prevent ignition from heat or sparks. |
Training for Personnel | Provide training for personnel on the risks, handling procedures, and maintenance of explosion-proof lighting to ensure safety. |
Grounding and Bonding | Ensure all components are properly grounded to minimize the risk of static electricity buildup and electrical faults. |
Use of Certified Components | Only use certified components such as switches, connectors, and wiring that are tested for explosion-proof environments. |
Proper Labeling and Signage | Clearly mark hazardous zones and explosion-proof fixtures with appropriate warning labels and symbols to ensure safety awareness. |
Emergency Shutdown Systems | Implement emergency shutoff systems to isolate the lighting in case of electrical fault or explosion to reduce risk. |
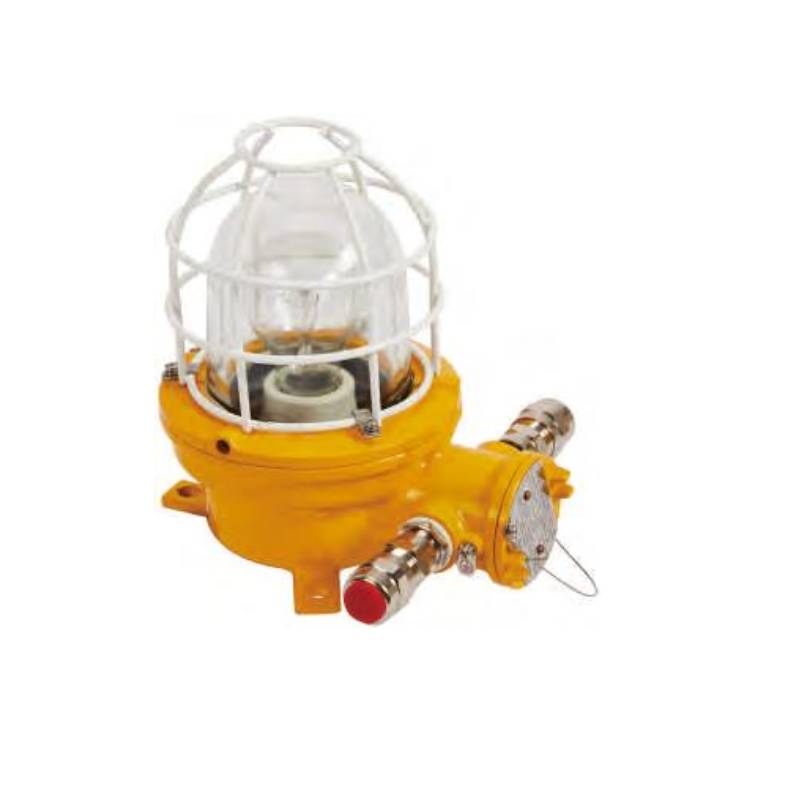
Final Thoughts
Zoning and classification are essential to the safe and effective use of explosion-proof lighting in marine environments. Whether navigating the complex cargo decks of an oil tanker or managing lighting on an offshore rig, selecting explosion-proof lights that meet the precise zone and environmental requirements ensures compliance, safety, and operational reliability.