How to Install Explosion-proof Lights in Marine Environments Properly
Marine environments present unique challenges for lighting installations, particularly in hazardous areas where flammable gases, vapors, or combustible dust may be present. Explosion-proof lights are essential in such settings to ensure safety and compliance with international marine safety regulations. Proper installation of explosion-proof lights in marine environments enhances operational safety, minimizes risks, and ensures longevity despite harsh conditions.
Table of Contents
Understanding the Need for Explosion-proof Lighting in Marine Environments
Hazardous marine environments, such as oil rigs, chemical tankers, and fuel storage areas, present significant risks due to the presence of volatile substances. Standard lighting fixtures can pose a serious safety threat if they generate sparks, excessive heat, or electrical malfunctions. Explosion-proof lights are specifically designed with reinforced enclosures that prevent ignition sources from coming into contact with flammable materials, ensuring a safe working environment.
Beyond explosion risks, marine conditions expose lighting systems to harsh elements, including saltwater, extreme temperatures, and strong vibrations. These factors necessitate the use of corrosion-resistant, weatherproof, and highly durable lighting solutions that can withstand the demanding conditions of offshore and onboard installations.
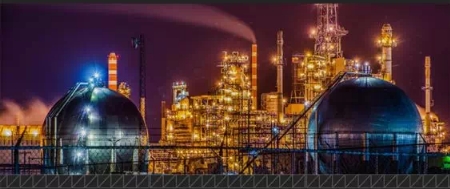
Key Considerations for Installing Explosion-Proof Lights
This chart provides key considerations in installing process, ensuring that explosion-proof lighting systems in marine environments remain safe, efficient, and compliant with industry standards.
Category | Key Considerations |
Hazardous Area Classification | Identify the zone (0, 1, or 2) based on the presence of flammable gases or vapors. Ensure compliance with safety regulations such as ATEX, IECEx, and UL844. |
Material Selection | Use corrosion-resistant materials like marine-grade aluminum or stainless steel to withstand saltwater and humidity. |
Ingress Protection (IP) Rating | Select fixtures with an IP66 or higher rating to prevent water and dust ingress. |
Thermal Management | Ensure the lights have heat dissipation features to prevent overheating, especially in enclosed areas. |
Mounting and Vibration Resistance | Secure fixtures with anti-vibration mounts to withstand continuous ship movement and mechanical stress. |
Electrical Safety | Use explosion-proof conduits, sealed junction boxes, and proper grounding to prevent ignition risks. Verify voltage compatibility with the vessel’s power system. |
Compliance and Certifications | Ensure fixtures meet international safety standards for marine hazardous environments. Check for ATEX, IECEx, or UL listings. |
Maintenance and Inspection | Conduct regular inspections for corrosion, water ingress, and mechanical wear. Replace damaged seals, LED modules, or enclosures as needed. |
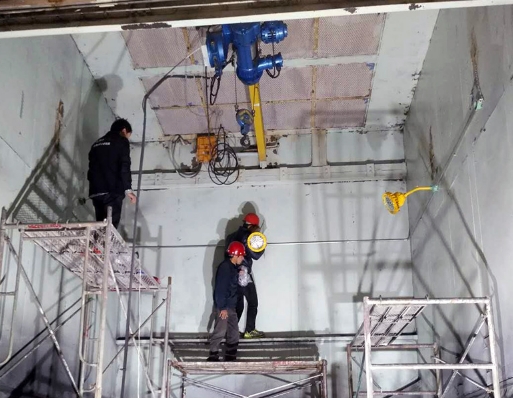
Challenges in Installing Marine Explosion-proof Lights
1. Environmental Challenges
One of the biggest challenges in marine environments is exposure to saltwater, which accelerates corrosion of metal components. Standard materials can deteriorate quickly, compromising the integrity of explosion-proof enclosures. To counteract this, lighting fixtures must be constructed from marine-grade aluminum, stainless steel, or non-corrosive coatings. Additionally, constant moisture and high humidity increase the risk of electrical faults, making it essential to use high IP-rated enclosures and sealed connections.
Temperature fluctuations also pose a challenge, especially in enclosed spaces like engine rooms where heat buildup can affect lighting performance. Explosion-proof lights must be equipped with proper thermal management systems to prevent overheating and maintain consistent illumination.
2. Installation and Mounting Challenges
Marine environments subject lighting systems to continuous vibrations from engines, waves, and machinery. These vibrations can loosen fasteners, damage wiring, and reduce fixture lifespan. To ensure stability, lights must be installed using anti-vibration mounts and secure fastening techniques. Additionally, proper placement is crucial to prevent excessive glare while ensuring adequate illumination of key operational areas.
Wiring installation is another major concern. Explosion-proof lights require specialized wiring systems with conduits that prevent gas leaks or electrical sparks. These conduits must be properly sealed and grounded to eliminate potential ignition sources. The complexity of running explosion-proof wiring in confined spaces or through hazardous zones further complicates installation.
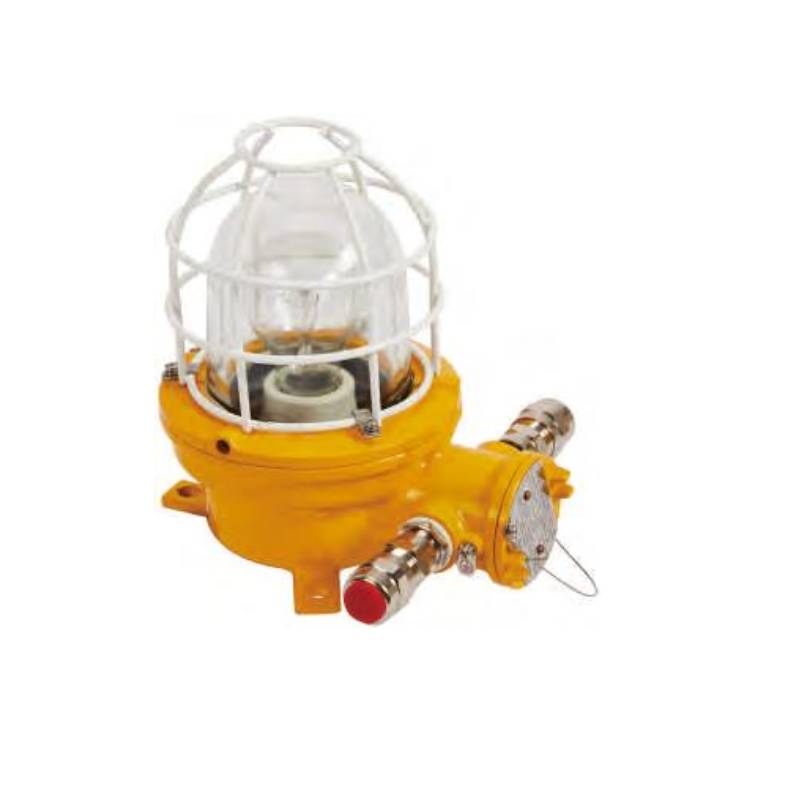
3. Regulatory and Compliance Challenges
Strict marine and industrial safety regulations must be met when installing explosion-proof lights. These include certifications such as ATEX, IECEx, and UL844, which dictate the design, testing, and performance of explosion-proof fixtures. Compliance requires selecting the right lighting solutions for the designated hazardous zone classification (Zone 0, 1, or 2). Failure to meet these regulations can result in operational shutdowns, fines, or increased safety risks.
Additionally, different vessels and offshore platforms may have varying compliance requirements based on regional or international standards. Ensuring that all explosion-proof lighting components are approved for the specific operational environment can add complexity to the selection and installation process.
4. Maintenance and Longevity Challenges
Even after installation, maintaining explosion-proof lights in marine environments is challenging. Regular inspections are required to check for corrosion, water ingress, and mechanical damage. Cleaning must be performed using non-corrosive solutions to prevent material degradation. Replacing worn-out components, such as gaskets or LED modules, can be difficult due to restricted access to lighting fixtures in hazardous zones.
Furthermore, the high cost of explosion-proof lighting systems means that operators must balance safety with budget constraints. Investing in high-quality, durable lighting solutions can minimize long-term maintenance costs but requires careful selection during the initial installation phase.
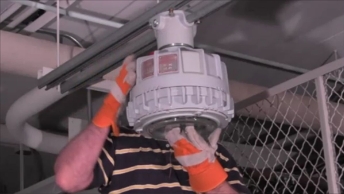
Best Practices for Installing Explosion-proof Lights in Marine Environments
1. Assessing Hazardous Area Classification
Before installation, it’s critical to evaluate the marine environment and classify the hazardous areas. Understanding the specific zones (such as Zone 0, Zone 1, or Zone 2) helps determine the required lighting for that area. Each zone has its own level of risk, based on the frequency and concentration of flammable gases or vapors. This classification ensures that only appropriately certified lighting is used, meeting strict safety regulations.
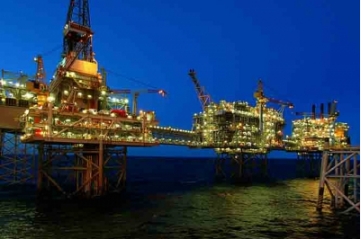
2. Selecting Certified Explosion-Proof Fixtures
Choosing lights that are specifically certified for hazardous areas is essential. Lights should have certification marks such as ATEX, IECEx, or UL844, which guarantee that they can operate safely in explosive atmospheres without causing ignition. In marine environments, the fixtures should be made from materials that are highly resistant to corrosion, such as marine-grade aluminum or stainless steel, to withstand prolonged exposure to saltwater and other environmental elements.
3. Ensuring Proper Ingress Protection
Lighting fixtures need to be protected from water and dust ingress, which is particularly critical in a marine setting. Look for explosion-proof lighting fixtures with high IP ratings (such as IP66 or IP67), which ensure the lights are sealed against moisture and particles. This prevents corrosion and ensures reliable operation in wet or harsh conditions, such as when lights are exposed to rain or sea spray.
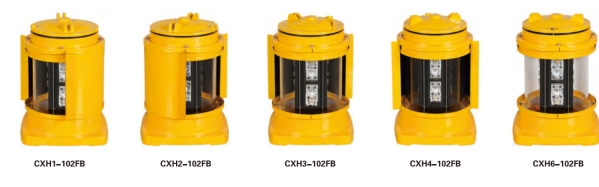
4. Mounting and Positioning
Proper mounting and positioning of explosion-proof lights is crucial for both safety and functionality. Fixtures should be securely mounted to prevent shifting or damage from the vessel’s movements. Anti-vibration mounts or supports should be used in areas where constant motion is expected, such as engine rooms or areas subject to machinery vibrations. Additionally, ensure that the lights are positioned to provide optimal illumination without obstructing critical views or equipment.
5. Using Explosion-proof Wiring Systems
The wiring used for explosion-proof lighting systems must also meet stringent safety standards. Wiring should be housed in explosion-proof conduits and secured with proper sealing methods. Any electrical connections must be sealed and grounded correctly to prevent the risk of sparks or short circuits. It’s essential to use explosion-proof junction boxes to protect wiring from environmental damage and to maintain system integrity in the event of a fault.
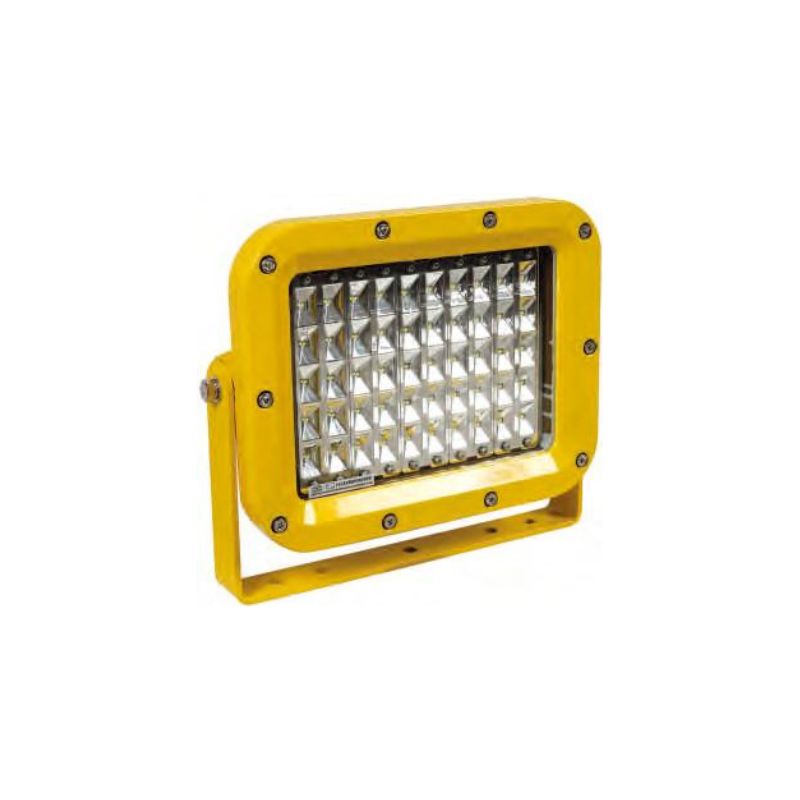
6. Managing Heat and Thermal Concerns
Explosion-proof lights can generate significant heat, especially in enclosed or poorly ventilated areas. It’s essential to select lighting systems designed with effective heat dissipation features, such as cooling fins or thermal management designs. Overheating can lead to system failure or even increased risk of ignition, so ensuring that the lights do not overheat is a key consideration.
7. Planning for Easy Access and Regular Maintenance
Installation should allow easy access for ongoing maintenance and inspections. Explosion-proof lights must be regularly checked for signs of corrosion, water ingress, or physical damage. Seals and protective components should be inspected to ensure they remain intact and functional. Regular maintenance helps identify potential issues before they become safety hazards.
8. Verifying Installation with Post-Installation Testing
Once the lights are installed, conduct thorough testing to verify that they are functioning correctly and meeting the required safety standards. Check for proper illumination, secure electrical connections, and overall operational efficiency. Any issues identified should be rectified before the lighting system is put into operation.
9. Proper Documentation and Labeling
Document every step of the installation process, including certification details, installation dates, and maintenance schedules. This documentation is vital for safety audits and inspections. Additionally, all fixtures should be clearly labeled with their respective classifications, providing quick reference to technicians for maintenance or troubleshooting.
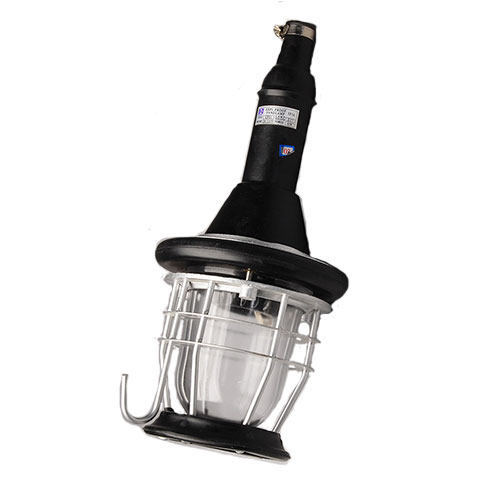
To sum up, the installation of explosion-proof lights in marine environments requires careful planning, selecting appropriate materials, adherence to safety standard and proper maintenance to ensure long-term performance. By following these best practices, installing marine explosion-proof Lights can be done effectively, ensuring both safety and reliability in hazardous areas.